Caterpillar® 14H Motor Grader The 14H blends productivity and durability to give you the best return on your investment. Power Train The field-proven 3306 engine offers exceptional lugging performance and fuel efficiency. The direct drive, power shift transmission features smooth, on-the-go shifting. To maximize productivity, it has eight. CAT 14H motor grader 2003 29,000hrs All runs and drives ok, slight issue with slider blade blade. Full report available. Tyre 30%, more photos and videos available via what's app £70,000.
Arcon domus 3d gratis online. INSTANT DOWNLOAD (add to cart)
Complete workshop & service manual with electrical wiring diagrams for Caterpillar 12H, 140H & 160H Motor Graders. It's the same service manual used by dealers that guaranteed to be fully functional and intact without any missing page.
This Caterpillar 12H, 140H & 160H Motor Graders service & repair manual (including maintenance, overhaul, disassembling & assembling, adjustment, tune-up, operation, inspecting, diagnostic & troubleshooting…) is divided into different sections. Each section covers a specific component or system with detailed illustrations. A table of contents is placed at the beginning of each section. Pages are easily found by category, and each page is expandable for great detail. The printer-ready PDF documents work like a charm on all kinds of devices.
FILELIST:
RENR1417 – Systems Operation (120H, 12H, 135H, 140H, 143H, 160H & 163H Motor Graders Air System & Brakes)
RENR1417 – Testing & Adjusting (120H, 12H, 135H, 140H, 143H, 160H & 163H Motor Graders Air System & Brakes)
RENR1418 – Specifications (12H, 140H & 160H Motor Graders Air System & Brakes)
RENR1430 – Schematic (12H, 140H & 160H Motor Grader Hydraulic System)
RENR1436 – Schematic (12H, 140H & 160H Motor Graders (Standard Version) Electrical System)
RENR9540 – Schematic (12H, 140H &160H Motor Grader Electrical System (for SN 4ER1136-UP, 5HM3000-UP, 2FM909-UP) All Other SN 1_UP)
SENR6998 – Specifications (12H, 140H, 143H, 160H & 163H Motor Graders Power Train)
SENR8503 – Systems Operation (120H, 12H, 135H, 140H, 143H, 160H & 163H Motor Graders Power Train)
SENR8503 – Testing & Adjusting (120H, 12H, 135H, 140H, 143H, 160H & 163H Motor Graders Power Train)
SENR8503 – Troubleshooting (120H, 12H, 135H, 140H, 143H, 160H & 163H Motor Graders Power Train)
SENR8539 – Disassembly & Assembly (12H, 140H & 160H Motor Graders Engine Supplement)
SENR8548 – Disassembly & Assembly (12H, 140H & 160H Motor Graders Power Train)
SENR8549 – Disassembly & Assembly (12H, 140H & 160H Motor Graders Machine Systems)
SENR8571 – Schematic (12H, 140H &160H Motor Grader Standard Version Hydraulic System (for SNs 2FM1-399, 5HM1-1149, 8JM1-279, 9JM1-349, 4ER1-499) All Other SN 1-UP)
SENR8623 – Specifications (12H, 140H & 160H Motor Graders Hydraulic & Steering System)
SENR8669 – Specifications (12H, 140H & 160H Standard Version Motor Graders Air System…)
SENR9149 – Schematic (12H, 140H &160H Motor Grader Standard Version Electrical System (for SN 4ER500-1135, 8JM280-UP, 5HM1150-2999, 9JM350-UP, 2FM400-908)
SENR9156 – Specifications (12H, 140H, 143H, 160H & 163H Motor Graders Power Train)
SENR9159 – Systems Operation (120H, 12H, 135H, 140H, 143H, 160H & 163H Motor Graders)
SENR9159 – Testing & Adjusting (120H, 12H, 135H, 140H, 143H, 160H & 163H Motor Graders)
SENR9178 – Specifications (12H, 140H, 143H, 160H & 163H Motor Graders Hydraulic and Steering System)
SENR9186 – Systems Operation (120H, 12H, 135H, 140H, 143H, 160H & 163H Motor Graders Hydraulic & Steering System)
SENR9186 – Testing & Adjusting (120H, 12H, 135H, 140H, 143H, 160H & 163H Motor Graders Hydraulic & Steering System)
SENR9186 – Troubleshooting (120H, 12H, 135H, 140H, 143H, 160H & 163H Motor Graders Hydraulic & Steering System)
RENR9540 – Schematic (12H, 140H & 160H Motor Grader Electrical System).pdf
RENR9571 – Schematic (12H, 140H & 160H Motor Graders Standard Versions Hydraulic System).pdf
SENR8518 – Systems Operation (120H,135H,12H,140H,160H,143H,163H MG HYD System & Steering).pdf
SENR8518 – Testing & Adjusting (120H,135H,12H,140H,160H,143H,163H MG HYD System & Steering).pdf
SENR8670 – Systems Operation (120H, 135H, 12H, 140H & 160H Standard Version Motor Graders).pdf
SENR8670 – Testing & Adjusting (120H, 135H, 12H, 140H & 160H Standard Version Motor Graders).pdf
EXCERPT:
11. Remove carriage assembly (2) from the ripper assembly. The weight of carriage assembly (2) is 500 kg (1100 lb).
Illustration 6
12. Position a suitable lifting device to link assembly (7). Remove bolts (10) and the locknuts from mounting pins (12).
13. Remove mounting pins (12) toward the center of the ripper until shims (11) and link assembly (7) are free of the ripper mounting bracket.
14. Remove link assembly (7) from the ripper mounting bracket. The weight of link assembly (7) is 132 kg (290 lb).
…
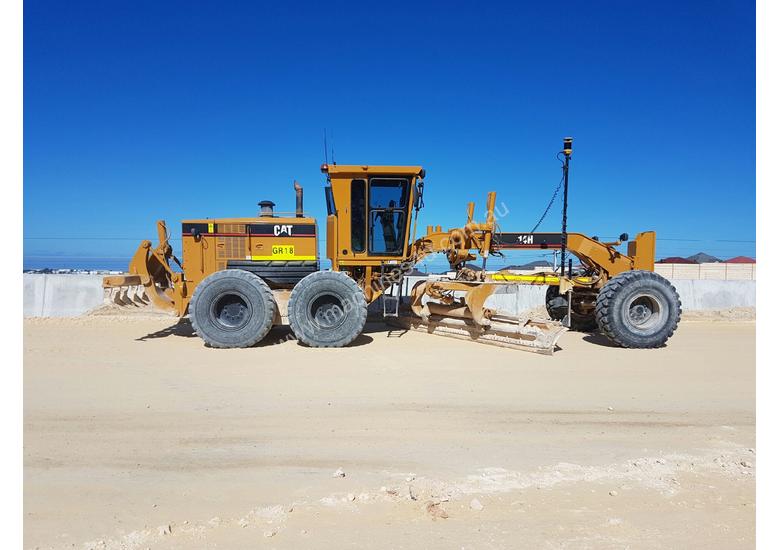
The drive shaft rotates between the torque converter and the transmission whenever the engine is running. Contact with the rotating shaft can result in personal injury or death. The rotating shaft is located under the implement and steering pumps. Do not allow personnel into the pump bay area behind the cab when the engine is running. |
Sudden movement or accidental starting of the machine can cause personal injury or death to persons on or near the machine. To prevent personal injury or death, perform the following: Park the machine on a smooth, level surface. Lower the work tool to the ground and engage the parking brake. Stop the engine and remove the key. Block the wheels and install the steering frame lock. |
The fan drive pump is a variable displacement piston pump. There is no pressure relief valve in the fan drive system. The pressure and flow compensator valve on the pump controls the pump cutoff pressure. The pressure and flow compensator valve also controls the flow of hydraulic oil to the fan drive motor.
The Caterpillar Electronic Technician (ET) software must be used in order to override fan speed solenoid (5). Caterpillar ET will then provide the correct control pressure to the pump control. The fan speed solenoid is controlled by the engine ECM.

EXCERPT:
11. Remove carriage assembly (2) from the ripper assembly. The weight of carriage assembly (2) is 500 kg (1100 lb).
Illustration 6
12. Position a suitable lifting device to link assembly (7). Remove bolts (10) and the locknuts from mounting pins (12).
13. Remove mounting pins (12) toward the center of the ripper until shims (11) and link assembly (7) are free of the ripper mounting bracket.
14. Remove link assembly (7) from the ripper mounting bracket. The weight of link assembly (7) is 132 kg (290 lb).
…
The drive shaft rotates between the torque converter and the transmission whenever the engine is running. Contact with the rotating shaft can result in personal injury or death. The rotating shaft is located under the implement and steering pumps. Do not allow personnel into the pump bay area behind the cab when the engine is running. |
Sudden movement or accidental starting of the machine can cause personal injury or death to persons on or near the machine. To prevent personal injury or death, perform the following: Park the machine on a smooth, level surface. Lower the work tool to the ground and engage the parking brake. Stop the engine and remove the key. Block the wheels and install the steering frame lock. |
The fan drive pump is a variable displacement piston pump. There is no pressure relief valve in the fan drive system. The pressure and flow compensator valve on the pump controls the pump cutoff pressure. The pressure and flow compensator valve also controls the flow of hydraulic oil to the fan drive motor.
The Caterpillar Electronic Technician (ET) software must be used in order to override fan speed solenoid (5). Caterpillar ET will then provide the correct control pressure to the pump control. The fan speed solenoid is controlled by the engine ECM.
Note: Caterpillar ET is a software program that can be used on an IBM compatible personal computer.
Required Tools | ||
Part Number | Description | Quantity |
8T-0860 | Pressure Gauge | 1 |
6V-3989 | Unvalved Nipple | 1 |
1U-6602 | Photo-Tachometer | 1 |
Before proceeding to the test procedure that follows, complete the procedure: Testing and Adjusting, 'Machine Preparation for Troubleshooting'
Illustration 1 | g01062907 |
View of the components under the cab (1) Pressure tap for output pressure of the fan drive (2) Margin pressure adjusting screw (3) Locknut for margin pressure adjusting screw (4) Pump control valve (5) Fan speed solenoid (6) Cutoff pressure adjusting screw (7) Locknut for Cutoff pressure adjusting screw (8) Fan drive pump |
The fan drive pump is located in the front of the pump compartment. The pump compartment is on the front frame under the operator compartment. The fan drive pump is in line with the hydraulic and steering pump.
14h Cat Grader Specs
- Engage the parking brake.
- Attach an unvalved nipple to a 0 to 16000 kPa(0 to 2321 psi) pressure gauge. Attach a section of hydraulic line to the unvalved nipple. Attach the hydraulic line to pressure tap (1).
- Shift the transmission to neutral.
- Start the engine. Run the engine at high idle.
- Move the wheel lean cylinder to the end of the stroke. Stall the cylinder. At the same time, circle the moldboard. This will warm the hydraulic oil to normal operating temperature of approximately 60° ± 5°C(140° ± 9°F).
- Connect Caterpillar ET to the data link connector. The data link connector is located on the front face of the shift console. Start Caterpillar ET.
- Select the 'File' menu. From the 'File' menu, select the engine 'Electronic Control Module (ECM)' for your machine. Select 'Diagnostics'. Select 'Diagnostic Tests'. Select 'Override Parameters'. Select 'Engine Fan Bypass'.
- Enter '0%' for the 'Engine Fan Bypass Override Parameter'. Press 'Enter' until all warning messages disappear. This will cause the fan to run at maximum speed when the engine is at high idle.
- With the engine at high idle, use the 1U-6602 Photo-Tachometer in order to measure the fan speed. The pressure reading of the pressure gauge should be used as reference only. Use the following table in order to determine the correct fan speed and reference pressure.
Table 2
Fan Speeds Model Fan Speed Reference Pressure 14H 1210 ± 25 RPM 8000 ± 500 kPa(1160 ± 73 psi) 14H High Ambient 1350 ± 25 RPM 10000 ± 500 kPa(1450 ± 73 psi) 16H 1350 ±25 RPM 10000 ± 500 kPa(1450 ± 73 psi) 16 High Ambient 1470 ±25 RPM 11840 ± 500 kPa(1717± 73 psi) - If the pump cutoff pressure of the fan drive pump is not correct, the cutoff valve must be adjusted.
- Stop the engine.
- Loosen locknut (7).
- Turn adjusting screw (6) clockwise in order to increase the pressure setting. Turn adjusting screw (6) counterclockwise in order to decrease the pressure setting.
- Tighten locknut (7).
- Start the engine.
- Repeat Step 7 through Step 15 until the proper fan speed is obtained.
- Use Caterpillar ET in order to reset the 'Engine Fan Bypass Override Parameter'.
- Exit the Caterpillar ET program and disconnect ET from the machine.